Le domaine d’outillage, que ce soit pour l’agriculture, les outils de coupe, les têtes de forages pour l’industrie pétrolière ou minière, ou tout simplement des forets de perceuse, a besoin d’assembler sur des corps acier des pièces dures et résistantes à l’abrasion.
C’est dans ce but que nous avons mis en place tout une gamme de brasures adaptées pour le brasage fort de métaux durs tels que les plaquettes carbures monobloc ou les diamants PCD. Deux gammes principales de produits sont disponibles : une gamme standard, ainsi qu’une gamme spécifique sous forme d’alliage multicouches pour compenser les tensions internes dans les pièces finales.
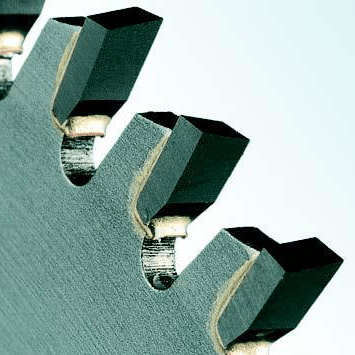
Qu’est-ce qu’une brasure sandwich ?
Comme leur nom le suggère, les métaux d'apport de brasage sandwich se caractérisent par leur structure sandwich. Le noyau est une couche intermédiaire avec une température de fusion plus élevée que la température de fusion de la brasure forte. Ce noyau est entouré normalement un métal d'apport de brasage à base d'argent de chaque côté. Leur rapport d'épaisseur standard est de 1 : 2 : 1 (métal d'apport de brasure : couche intermédiaire : métal d'apport de brasure). D'autres rapports d'épaisseur sont également disponibles. Vous pouvez voir ici une vue au microscope d’une coupe de brasure BrazeTec 49/Cu avec un zoom de 250.
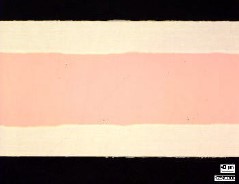
Qu'est-ce qu'un métal dur ?
Les métaux durs sont des matériaux frittés comprenant un ou plusieurs matériaux durs noyés dans une matrice-liant métallique. Les différentes compositions, microstructures et technologies de fabrication signifient qu'une large gamme de métaux durs aux propriétés diverses est actuellement disponible dans le commerce. De nombreux métaux durs, en particulier ceux qui présentent la plus haute résistance à l'usure et la plus grande ténacité, sont presque exclusivement composés de carbure de tungstène avec du cobalt comme liant métallique. Ils sont vendus sous la forme de plaquettes carbure monobloc, ou sous forme de composites cobalt diamant. Le spectre de propriétés peut être élargi en utilisant d'autres carbures tels que TiC.
Les paramètres qui déterminent les performances des métaux durs sont essentiellement : la dureté, la dureté à haute température, la résistance ultime à la flexion, la résistance à la diffusion et à l'oxydation et la résistance aux chocs thermiques.
Un métal dur idéal combine les propriétés opposées d'une dureté élevée et d'une résistance à la flexion ultime élevée. Les développements dans le domaine des métaux durs et de la technologie de fabrication ont abouti à de nouveaux métaux durs à grains fins ayant une dureté élevée sans nuire à la ténacité.
Pourquoi utiliser une brasure sandwich multicouche ?
Le rôle de la couche intermédiaire en cuivre ou en alliage spécial est d'absorber les contraintes pouvant survenir lors de la phase de refroidissement. Un treillis en nickel peut également être mis en place comme espaceur qui garantit que l'écart entre l'acier et le carbure cémenté est d'une largeur constante et reproductible.
Lors de l'utilisation des outils, le joint brasé doit résister aux forces qui agissent et il ne doit y avoir aucun dommage au joint. Les joints brasés ne doivent pas introduire de pics de contraintes dans le métal dur le faisant risquer de se rompre. Ceci est obtenu en utilisant des intervalles de brasage plus grands et des alliages de brasage tri-métalliques. L'espace de brasage doit avoir une épaisseur constante sur toute la zone du joint afin de permettre une liaison efficace et une utilisation de la capillarité. A cet effet, le métal dur et le porte-outil en acier inox ou acier spécial doivent avoir le même contour dans la zone de jointure. En fonction des composants à assembler, de l'alliage de brasage utilisé et de la qualité du joint brasé résultant, la zone du joint peut avoir une résistance mécanique à des forces de cisaillement d'environ 150-300 MPa.
Vous pouvez voir une simulation de contrainte dans le carbure cémenté après refroidissement d'un composé carbure cémenté/acier réalisé avec un métal d'apport de brasage sandwich. Le bleu foncé marque les zones sans aucune contrainte de traction, le rouge orangé marque les zones les plus sollicitées. De toute évidence, un métal d'apport de brasage sandwich dans la section médiane du carbure cémenté produit une zone beaucoup plus petite avec peu de contrainte de traction qu'un métal d'apport de brasage conventionnel. De plus, le côté du carbure cémenté est exposé à des forces considérablement plus faibles.

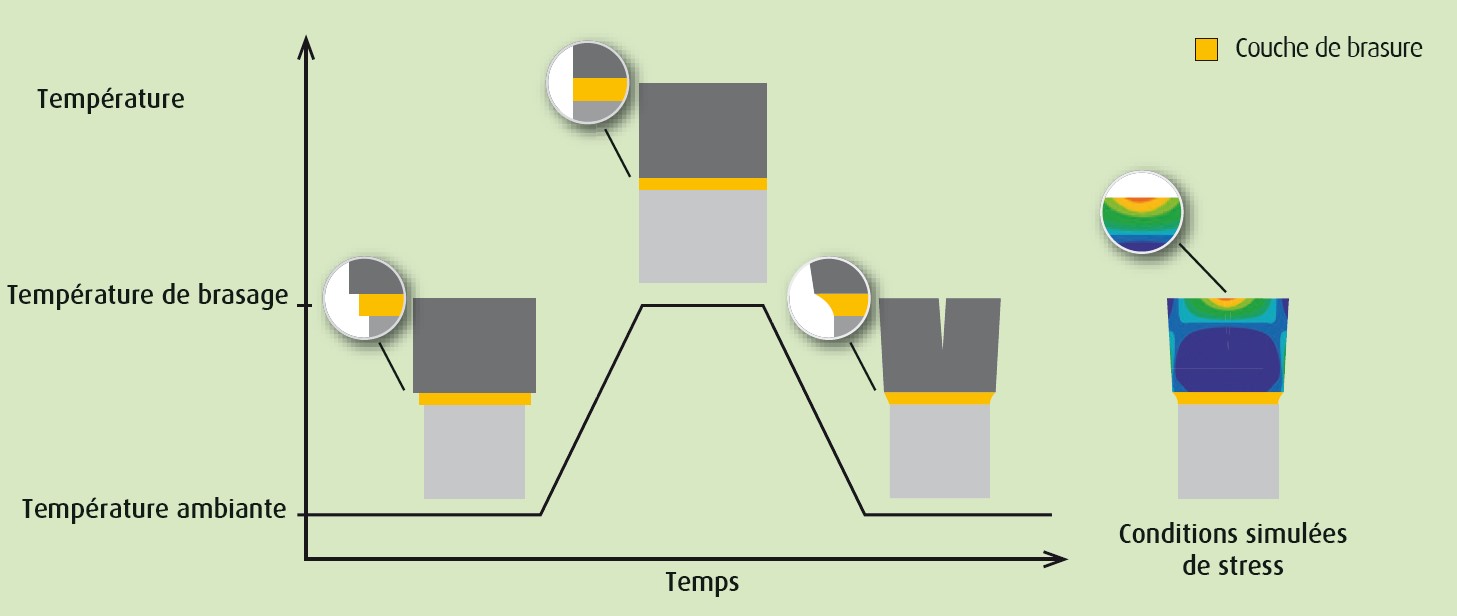
Quelles règles respecter pour un bon brasage de carbures et de PCD ?
En raison des coefficients de dilatation thermique très différents du métal dur et de l'acier, des contraintes surviennent lors du refroidissement en raison du retreint dû à la contraction thermique. Cela peut entraîner une déformation du composant et des fissures dans le métal dur. A la température de brasage, le composite est initialement exempt de contraintes. Pendant le refroidissement, l'acier se contracte deux fois plus que le métal dur, provoquant un gauchissement du composant. La conséquence en est une contrainte de traction à la surface du métal dur. Dans des situations défavorables, cela provoque le développement de fissures et une diminution de la durée de vie de l'outil et des pièces d’usure.
La quantité de stress dépend de :
- La différence des coefficients de dilatation thermique ;
- La température de solidus et le point de fusion de l'alliage de brasage ;
- La déformabilité plastique de la brasure ;
- L'épaisseur du cordon d'alliage de brasage ;
- La géométrie des pièces à assembler, notamment la taille du composant ;
- Les propriétés mécaniques du support en acier ou acier inoxydable.
Les options pour diminuer le stress sont :
- Utiliser un alliage de brasage avec une température de solidus aussi basse que possible ;
- S'assurer que l'épaisseur de la couche d'alliage de brasage est adéquate ;
- Utiliser des alliages de brasage sandwiches tri-métallique, (Couche Cu, maille nickel).
Utilisation de brasures argent pour diminuer la température de brasage
L'utilisation d'alliages de brasage à l'argent sans cadmium et sans plomb permet d'utiliser des températures de brasage nettement plus basses que lorsque des alliages de brasage à base de cuivre sont utilisés. Le brasage est principalement réalisé soit par induction, soit à la flamme dans l'air. La basse température de brasage, dépendant de la teneur en argent, réduit la contrainte maximale qui se produit dans le métal dur. En augmentant le jeu de brasage, une partie de la contrainte peut être dissipée par déformation plastique de l'alliage de brasage.
Si les outils doivent être revêtus après le brasage avec du TiN afin d'augmenter leur durée de vie, un alliage de brasage à l'argent sans zinc approprié doit être utilisé pour le brasage (BrazeTec 6488, BrazeTec 64/Cu). En raison de la pression de vapeur plus faible du zinc et de la température de surface pouvant atteindre 500 °C pour le processus de revêtement PVD, le zinc s'évapore pendant le traitement sous vide. Outre la perte de précision dimensionnelle, cela provoque une perte de résistance du joint brasé et une contamination du four à vide avec du zinc.
L'utilisation d'alliages de brasage sans zinc est également recommandée pour le brasage au four. Il faut mieux dans ce cas travailler sous vide, ou sous atmosphère inerte, azote ou argon. Les temps de brasage relativement longs pour le brasage au four provoquent l'évaporation du zinc.
Utilisation de brasures sandwiches pour diminuer les contraintes mécaniques
Les alliages de brasage tri-métalliques sandwiches sont largement utilisés pour les outils de brasage. Ils combinent les bonnes propriétés de déformation plastique du cuivre avec la basse température de travail des alliages de brasage à l'argent. Une couche intermédiaire de cuivre est plaquée des deux côtés avec un alliage de brasage à l'argent (BrazeTec 49/Cu ou 64/Cu). Lors du refroidissement après brasage, la contrainte est réduite du fait de la déformation plastique de la couche intermédiaire de cuivre qui est relativement molle par rapport à la brasure et aux composants à assembler. En conséquence, le métal dur reste exempt de tension. Pour les surfaces de brasage supérieures à environ 100 mm², les métaux durs ne peuvent être brasés sans contrainte qu'avec des alliages de brasage trimétalliques. Selon la géométrie et l'application, les alliages de brasage trimétalliques sont également utilisés pour les zones de brasage plus petites.
Un type d’alliages de brasage trimétalliques spécifique est celui à mailles de nickel. Lors du brasage, l'alliage de brasage qui est incorporé dans le treillis fond. Le maillage en nickel non fondu maintient les composants à assembler à une largeur d'écart constante. Lors de la solidification, il y a une dissipation des contraintes due à la déformation plastique de l'alliage de brasage
Quels flux utiliser lors de l'assemblage d’aciers et carbures ou pièces diamantées ?
Pour un mouillage réussi des composants assemblés par brasage, il est nécessaire d'avoir une surface exempte d'oxyde. Le flux décapant pour différents domaines d'application diffère en ce qui concerne la température de travail, les propriétés spécifique du métal à s’oxyder et leur consistance en fonction du mode d'addition. Il est néanmoins suggéré d’utiliser des flux ayant une résistance à la température élevée et longue, tels que les flux BrazeTec Special h, BrazeTec s et BrazeTec Special s. Tous les flux de la gamme de produits BrazeTec sont conformes à la norme DIN EN 1045.
Quels sont les domaines d’activité qui utilisent les carbures, aciers durs et produits diamantés ?
L’utilisation d’aciers durs est très souvent liée à des activités nécessitant une action d’érosion de la matière comme par exemple la découpe, forage, perçage, malaxage. Les brasures pour métaux durs et les brasures sandwiches sont utilisées dans l’industrie de l’outillage, dans l’agriculture, dans le forage...